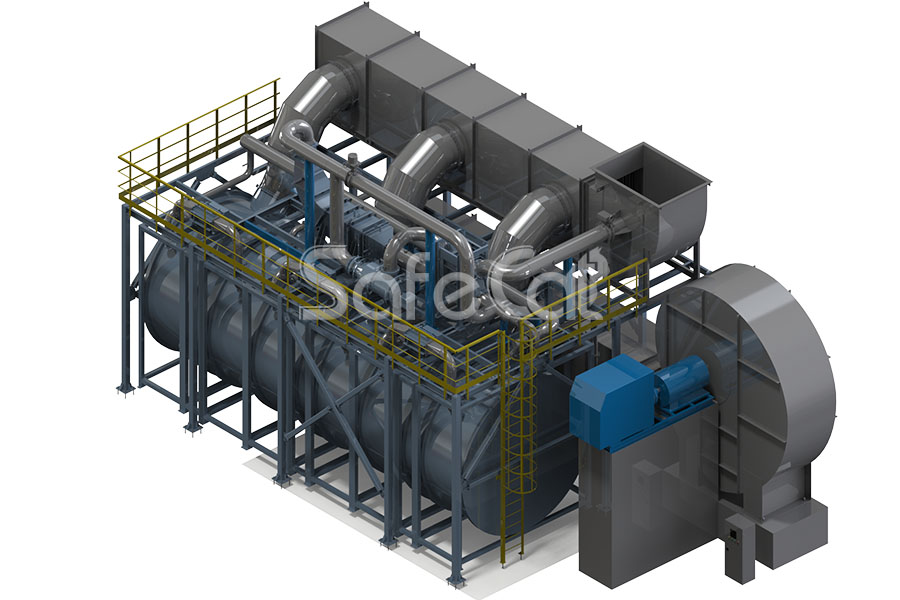
Advantages
Degree of purification
- No less than 95%
- Volume = less than 2 g/m3 (by C5)
Pollutants
- VOCs (aldehydes, alcohols, ketones, etc.)
- CO (carbon monoxide)
- Products of incomplete combustion
Capacity
- From 5000 up to 200 000 Nm3/hr
-
Application
SC catalytic treatment plant with rotary concentrator. Purpose:
-
purification of low content contaminated emissions in ventilation systems of industrial facilities (plants of rubber products, coating materials enterprises, pharmaceutical plants), etc.
SC catalytic treatment plant is used for purification of industrial emissions from the following contaminants:
- carbon monoxide (CO)
- Volatile Organic Compounds (VOCs)
-
benzene, toluene, xylene, phenol, formaldehyde, methanol, butyl acetate, acetone, acetic acid, styrene and other saturated, unsaturated, cyclic, aromatic hydrocarbons and their derivatives (alcohols, aldehydes, ketones, etc.)
-
chloromethane, chlorobenzene, methyl chloride and other organic compounds.
For the optimal selection of the required SC plan module, use the Table of the main sources of industrial emissions.
-
-
Operating principle
STAGE 1. Rotary concentrator. Concentration of organic substances in the flow.
Most of the contaminated air is directed from the fan (1) to the adsorption section of the rotary concentrator filled (2) with adsorbent.
VOCs are absorbed by adsorbent when gas flow enters concentrator.
-
After adsorption the purified air is discharged into the atmosphere.
-
Part of the contaminated air with a significantly lower flow rate enters the cooling section of the rotary concentrator where the adsorbent is cooled after its regeneration. Then the flow is heated by electric heaters (3) and enters the desorption section of the rotor concentrator, where the adsorbent is regenerated.
-
The process temperature ensures the desorption of all absorbed substances.
-
Due to the difference in volume flow rates, but similarity of the mass flow rate of the pollutant, the concentration in the regenerated stream increases.
-
Air with desorbed substances is directed by a fan (4) to the catalytic oxidation module for cleaning.
STAGE 2. Afterburner. Catalytic neutralization.
-
The prepared gas-air mixture is fed into the plate heat exchanger* (5), where it is heated by the heat of the purified stream exiting the catalytic unit through HX tubes.
-
The catalytic block (6) is preliminary heated by electric heaters** (7) to the process activation temperature.
-
The operational temperature of the incoming stream is ensured by the exiting gas heat recovery.
-
The process of oxidation of organic substances to harmless carbon dioxide and water is carried out on a platinum catalyst (6).
-
The purified gas is cooled in the recovery HX* (5) by the incoming stream and then discharged into the atmosphere.
Advantage of the basic module of the SC plant with rotary concentrator:
To maintain the necessary technological regime, low contaminant content polluted gas is concentrated for the cleaning process.
*The type of heat exchanger depends on the unit’s construction
** Replacement of heating elements with a gas burner is possible
-
-
Specifications
Name SC catalytic treatment plant Assembly SC catalytic treatment system (base module with rotary concentrator)
Capacity (of one unit) from 5000 up to 200000 Nм3/hr Package with the capacity from 5000 up to 70000 Nm3/hr
(position / dimensions, l+w+h*)
horizontal 14000х7500х8500 vertical 12000х6000х15000 Package with the capacity from 5000 up to 70000 Nm3/hr
(position / dimensions, l+w+h*)
horizontal 16000х7500х8500 vertical 12500х10000х15000 Hydrocarbon concentration less than 2 g/Nm3 (by С5) Cleaning efficiency no less than 95% *without taking into account exhaust pipe height
-
Photos
-
Video